In production-sensitive environments, such as pharmaceuticals, electronics, and food and beverage industries, there are stringent standards in place to ensure these manufacturing sites are pollutant-free.
When quality counts
The pharmaceutical industry is one of the most strictly regulated industries in the world.
Companies manufacturing medicines must abide by:
- Good Manufacturing Practice (GMP) protocol
- The European Pharmacopoeia
- Various guidelines from the Food and Drug Administration (FDA)
- Recommendations from the International Council for Harmonisation of Technical Requirements for Pharmaceuticals for Human Use (ICH3)
Compressed air is also a key utility supporting processes in the food and beverage industry, and strict standards and laws governing hygiene in food production apply. Under European food hygiene regulation 852/2004, for example, manufacturers have a duty of care to protect consumers from harmful or dangerous contaminants including oil and particles.
Pharmaceutical production
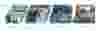